As a manager, owner or responsible person for production in a spray or preparation booth, you will need to understand the facility equipment needs to fulfil your targets, budgets and most importantly the customer satisfaction. Further, you, as the one in charge, needs to understand the building codes, laws and regulations with your spray or preparation booth. These varies from country to country.
Finally, you need to analyze and figure out the financial implications for further investments in your spray or preparation booth (from now on preparation booth will be describes as “spray booth” for the sake of simplification).
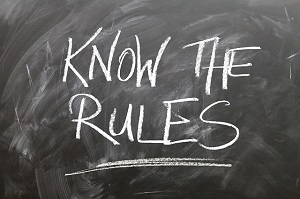
Four steps to understanding you needs within the spray booth
We will look at four steps you need to consider for optimizing your spray booth, working faster and safer, compared to traditional ways of working on your objects. More on to the point – using man lifts instead of scaffolds and ladders. As the spray booths are classified as an ATEX-zone, you will need to consider safe man lifts which complies to the requirements of working inside such an environment.
First, you need to have a clear understanding of the laws and regulations for work inside a spray booth and how work at height is to be done in both a practical way but also within the regulations for work at height (European Union’s directives and Occupational Safety and Health (OSH) in the US). The risk of not being in compliance with these regulations can effectively stop your production and result in fees until the violation is solved. And in the worst-case scenario, accidents.
Second, you will need to develop an in-depth understanding of what type of work being conducted in the spray booth. Is it only a few times you will be working at height inside the booth, or is it a recurring need? Understanding the frequency of when you need to work at height will help in evaluation in step three and four, and also the implications on the use of the given resources, time spent, safety aspects which finally determines your overall costs.
Thirdly, is to fully understand the need(s). Ask yourself, how much work do we do at height? How many of my personnel is involved when doing certain tasks on larger objects inside the booth? How much time do I need to spend organizing work on large objects? Are the safety aspects taken care of using my traditional scaffold or ladders? (in many cases they are not) And if the safety aspect is not taken care of, what would be the implications if an accident occurred or an inspection from Governmental agencies took place? What would the implications be if one or more of my workers got injured from falling from height? The latter is not only reflected in costs of workers on sick-leave and hiring in replacement work force, but also reflected in a quite large company-fine for violating norms, laws etc for work at height. Not being compliant could set back your business and production.
The fourth and final step, you will need to look into the vast numbers of suppliers of man lifts in the market today. Remember, you will need a special man lift to operate inside your booth as it is defined as an ATEX-zone (a zone where gases and fumes are present). The latter disqualifies 80-90% of the available suppliers (depends on your market and suppliers). A man lift is not just a “man lift” when it comes to doing work at height inside a spray booth. It needs to fulfil certain criteria, which you should be aware of based upon your research in “step one” above. What is set to be a minimum selection criterion are certifications for the man lift to operate in an ATEX-environment. Observe that many companies do their own certifications, which is OK as long as they follow the strict guidelines and laws. The best practice is when the manufacturer uses an independent third party to certify their products according to the laws and regulations (example TÜV, UL etc). Make sure the equipment you are buying is compliant and documented.
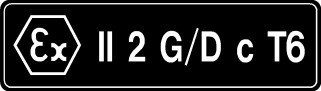
What is work at height?
What is work at height? It can be confusing where the boundaries are set. But on a general basis it means work in any place where, if precautions were not taken, a person could fall a distance liable to cause personal injury. From this definition, you are working at height if you:
- Work above ground/floor level
- Could fall from an edge, through an opening or fragile surface or,
- Could fall from ground level into an opening in a floor or a hole in the ground
Who are responsible for personnel working at height?
All duties are placed on the employers and those who control any work at height activity (ie facility managers). All work at height needs to be properly planned, and people involved in this works needs to be competent. The risks involved needs to be addressed and assessed, and properly work equipment must be selected and used. Equipment used for this line of work must also be properly inspected and maintained.

Choosing your man lift for your spray booth
First, when choosing your man lift, you need to define what type of man lift you need. Basically, you would need a lift which is certified to operate in an ATEX environment (where gases and fumes are present) in order to avoid any explosions or fires etc (remember that paint produce gases inside the spray booth).
Second, you need to define is whether you need a fix man lift (fixed to the wall or to the ground) or a self-propelled man lift. The two different types of man lifts have their advantages and disadvantages, which we will look into shortly.
A fixed man lift (to wall or ground)
You should certainly consider a fixed solution (wall or ground) if your booth is set up for a certain object with the same form factor every time as a part of a specific production line. Even if the object to be worked upon does not have the same form factor each time, a fixed man lift solution could be considered as long as the man lift operates on all axis – left/right, up/down and in/out. The variance in the object’s size (especially width) will be the deciding factor.
As you have the option of choosing: a man lift either fixed to the wall or to the ground, you would need to consider the pros and cons for those types of installations. The man lifts fixed to the ground, and running on a rails on the ground, will apply all the weight to the floor. Which in most cases will be no problem. And the upper part of the mast will be connected to a guiding rail on the wall. The disadvantage of these installations will be evident when the operator uses different kinds of tools in the basket, and the hoses are laying on the floor. These hoses can be run over, and one would/could have contamination of the booth and stop in the production. Further, the rails can in some cases be placed very close by the personnel door (along side the length of the booth), providing a place where personnel can stumble and in worst case be a hinder for an evacuation of the spray booth.
A man lift fixed to the wall will apply all weight to the wall. Normally these are fixed on bearing pillars or by the use of backplates evening out the forces applied to the wall. One of the advantages of having the man lift fixed on the wall is that it will not run over the hoses laying on the floor, as the lower parts of the man lift will not be in contact with the floor. The lower parts will be in contact with the wall (not the ground). Further, as there are no rails on the floor, there are no obstacles to stumble on or to block any evacuation from the spray booth.
However, if the form factor of the object does vary a lot, you may consider having a self-propelled man lift. The main advantages of a self-propelled man lift are that you can drive around in the spray booth even if the object is wide or not so wide (a fixed man lift solution may not reach the smallest objects). A self-propelled man lift can cover the whole object, as it can drive around the object. The disadvantage of using a self-propelled man lift is the limitation of upwards movement. The limitation is often based upon the need for stability. The higher you want to go, the more stability you would need, meaning the base element of a self-propelled needs to be wider, longer and heavier.
Should you have a pneumatical, electrical or hydraulic man lift in you spray booth?
Pneumatic man lifts, electrical man lifts, or hydraulic man lifts can all be used in a spray booth, but have different advantages and disadvantages, which will be discussed in this section. The differences involve both operational costs, maintenance costs and the initial investments.
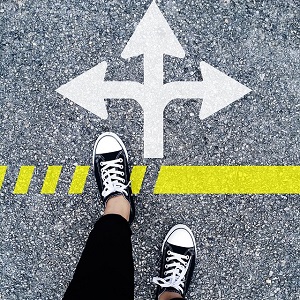
Electrical man lifts
Electrical man lifts need to be EX-proof. Normally these kinds of man lifts are only sold as self-propelled man lifts, and their energy source are batteries. They are normally quite heavy but have the capability to lift heavy loads. The main disadvantage of these man lifts is the fact that they usually have a high initial cost since the battery and the lift itself needs to be EX-proof (remember, working in an ATEX-environment). Second, at some point you would need to change this battery (they do not last forever), which means an additional investment during its life time. Even though these lifts are “plug and play”-solutions, the maintenance is not that easy, as it requires special competence to change various parts in order to be compliant. This also drives up the costs when looking at it from a maintenance perspective. As an advantage, we have mentioned that it can carry a quite heavy load compared to for instance pneumatic man lifts. Spare parts are considered expensive for these types of man lifts (special competence and parts).
Hydraulic man lifts
Hydraulic man lifts also have the capacity to lift higher loads as the electrical man lift. It has some similarities to the electrical man lift. This type of man lift will also need special competence to do maintenance on due to its complexity, which again drives the cost during it life time. One other aspect is that if there is a leak in the hydraulic system, oil can contaminate the object being worked at. Meaning that the spray booth needs to be cleaned down and all contamination needs to be removed. Further, if the oil is in contact with the object itself, one would also need to clean down the whole object as well. Costs related to contamination in a spray booth is considered to be high. Spare parts are also considered expensive for these types of man lifts (special competence and parts).
Pneumatic man lifts
Pneumatic man lifts are the most commonly used man lift for spray booths. These man lifts at its purest are ATEX-compliant, as they are driven by air only (NB! Some OEMs deliver hybrids solutions but labels the man lift as pneumatic man lift, which might complicate matters). The great advantage of pneumatic man lifts in comparison with other types of man lifts, are that these man lifts are inexpensive to use, they offer a clean operation (no messy oil spills), they are safe and quite easy to operate. The true beauty of pneumatic man lifts is that if it leaks, it does not contaminate or affect the environment, reducing the safety hazards of using such a system. It is a cost-effective system where a pressurized and sealed air system requires limited cleaning due to air as a power/energy source. In comparison, the spare parts are less expensive and can be changed with less competence than the other described man lifts. So even though these lifts might have an initial high cost, compared to the alternatives, the costs during its lifetime is much less. And over it lifetime produces less total costs.
Can’t just ladders and stepladders do the job for work at height?
Above we have discussed the use of man lifts for work at height inside a spray booth. You may now think is; “What is all this talk about man lifts? Can’t just ladders or stepladders do the job?”. Yes, in some case ladders and step ladders can do the job. However, you need to be aware and know some guiding rules about ladders in general.
Ladders can be used for work at height when a risk assessment has shown that using the equipment offering a higher level of fall protection is not justified because of the low risk and short duration of use; or there are existing workplace features which can’t be altered.
Duration or time is NOT the deciding factor in establishing whether an activity is acceptable or not – risk is.
As a thumb of rule, if you task would require staying up a leaning ladder of stepladder for more than 30 minutes, it is recommended that you consider alternative equipment.
Investment in a man lift vs the use of ladder, stepladders or scaffolding
An investment in a man lift will set you back temporally financially, compared to still hanging on to the old way of work at height inside a spray booth. The word temporally is used, as the advantages of using a man lift will over time prove to be a more financially good decision. A man lift will increase the efficiency inside a spray booth. Given that a booth is in constant use, the return on investment will normally take 3-4 years. It will also make sure that you are in compliance with norms and laws related to work at height. Further, the workers can work longer hours inside the cage of man lift compared to working from a ladder and leaning into different angels. The finishing is also true to be better with a man lift as the operator will be able to get a decent working position on the object which would also reduce overspray on certain parts of the object.
The longer the object is the more effectiveness you will gain inside a spray booth. Ie trains, buses are typical long and tall objects where a man lift would come to its true potential with respect to efficiency.
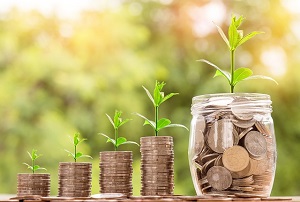
Reglo AS is an OEM of pneumatical man lifts
Reglo is an OEM of the pneumatical man lift Wall-Man, Wall-Man XL, Liftman and Liftman Fold. Reglo AS’ man lifts have been on the market for more than 30 years and have been exported to over 40 countries worldwide. All man lifts from Reglo are certified by a third-party notifying body (TÜV and UL), and are in compliance with the acting norms and laws. To review more about Reglo AS’ man lifts please visit these links below:
To learn more about where the man lifts can be applied, please visit our overview of the different segments.
To learn more about the certifications of the man lifts and ATEX-compliance, please check out the links below:
UL Wall-Man/XL and Liftman/Fold